Marsis Cabral Junior a , Paulo Brito Moreira de Azevedo b , Gláucia Cuchierato c , José Francisco Marciano Motta d
a Laboratório de Recursos Hídricos e Avaliação Geoambiental – LABGEO, Centro de Tecnologias Geoambientais, Instituto de Pesquisas Tecnológicas do Estado de São Paulo – IPT, São Paulo, SP, Brasil
b Coordenadoria de Planejamento e Negócios, Instituto de Pesquisas Tecnológicas do Estado de São Paulo – IPT, São Paulo, SP, Brasil
c GeoAnsata Projetos e Serviços em Geologia, São Paulo, SP, Brasil
d Consultor – Bolsista Fapesp, São Paulo, SP, Brasil
Resumo
Este trabalho deriva de estudo de maior abrangência dirigido à elaboração de um diagnóstico técnico-econômico da indústria cerâmica no estado de São Paulo, com vistas a subsidiar ações de governo que garantam o abastecimento sustentável de matérias-primas minerais a este setor da economia. Entre as cerâmicas tradicionais foram priorizados os segmentos industriais de maior relevância econômica no Estado e com consumo significativo de bens minerais, a saber: Cerâmica Vermelha, Revestimentos, Louça Sanitária, Louça e Porcelana – Mesa, Utilitários e Decoração, Colorifícios (Fritas, Esmaltes e Corantes), e Cerâmica Técnica – Isoladores Elétricos. Nesse contexto, as avaliações desses segmentos e a análise estratégica efetuadas buscaram estabelecer um arcabouço de informações, bem como sugestões de iniciativas para o fortalecimento do setor produtivo, que poderão auxiliar a formulação de políticas para modernização e aprimoramento do sistema de suprimento mineral ao parque cerâmico paulista.
Os principais resultados desse estudo serão tratados em uma série de quatro artigos. Este primeiro artigo aborda aspectos metodológicos, contextualização e fatos motivadores do estudo, breve histórico e características gerais da estrutura produtiva e de mercado da indústria cerâmica no Estado, sendo analisado especificamente o segmento de cerâmica vermelha. Os demais segmentos industriais, bem como a análise estratégica da cadeia produtiva mínero-cerâmica, serão apresentados nos artigos subsequentes.
Palavras-chave: cerâmica, matérias-primas, indústria, mineração, tecnologia
1. Introdução
Este trabalho decorre de estudo desenvolvido pelo Instituto de Pesquisas Tecnológicas do Estado de São Paulo (IPT, 2018) e financiado pela Subsecretaria de Mineração da Secretaria de Energia e Mineração - SEM do Estado de São Paulo, que envolveu a elaboração de um diagnóstico técnico-econômico da indústria cerâmica no Estado de São Paulo, com a finalidade de coletar subsídios que permitam orientar ações de governo que garantam o abastecimento sustentável de matérias-primas minerais necessárias a este setor da economia, a curto, médio e longo prazo.
Contido nesse escopo geral, o desenvolvimento do estudo contemplou as seguintes metas:
- caracterização qualitativa da estrutura de mercado e empresarial do elo central da cadeia produtiva cerâmica, isto é, do segmento de manufatura cerâmica, abrangendo os principais segmentos de manufatura cerâmica intensivos em consumo de minerais industriais, a saber: Cerâmica Vermelha, Revestimentos, Louça Sanitária, Louça e Porcelana de Mesa e Decorativa, Isoladores Elétricos e Colorifícios (fritas, esmaltes e corantes);
- projeções de consumo de bens minerais: estimativa de crescimento do parque cerâmico e da demanda derivada de insumos minerais, circunstanciada em três cenários de crescimento (pessimista, neutro e otimista);
- avaliação estratégica do setor cerâmico: indicações conclusivas sobre os principais fatores que interferem na competitividade da indústria cerâmica paulista e sugestão de diretrizes e ações para o aprimoramento competitivo, mormente relacionadas à demanda de bens minerais.
Este artigo aborda aspectos metodológicos, contextualização e fatos motivadores do estudo, breve histórico e características gerais da estrutura produtiva e de mercado da indústria cerâmica no Estado, sendo analisado especificamente o segmento de cerâmica vermelha. Os demais segmentos industriais, bem como a análise estratégica da cadeia produtiva mínero-cerâmica, serão apresentados em três artigos subsequentes.
2. Abordagem Metodológica e Atividades Desenvolvidas
O estudo valeu-se de amplo levantamento de dados secundários em bibliografia especializada, sítios na internet e, mais em especial, no acervo de informações contidas em relatórios técnicos do IPT. Com intuito de se obter dados primários sobre as tendências tecnológicas e de mercado do setor mínero-cerâmico, bem como uma visão do ambiente de negócios no estado de São Paulo, foram efetuadas visitas a empresas cerâmicas, mineradoras e fornecedores de matérias-primas, e entrevistas com executivos e especialistas, ligados a instituições governamentais e ao setor produtivo. Os estudos foram desenvolvidos em seis etapas, sintetizadas a seguir.
- Organização do projeto: estruturação da equipe executora; acertos conceituais e metodológicos, definição da estratégia de ação no andamento dos trabalhos, e articulações com instituições
- Levantamento de informações: pesquisa bibliográfica em literatura e revistas técnicas especializadas sobre a indústria cerâmica e mineração (tecnologia, mercado e meio ambiente), e em trabalhos técnicos disponíveis em sítios da internet, bem como coleta e análise de dados censitários do Ministério do Trabalho e Emprego - MTE (número de empresas e empregos) e sobre balança comercial do Ministério da Indústria, Comércio Exterior e Serviços - MDIC. Também foram consultados os acervos de associações técnico-científicas e empresariais, e da Federação das Indústrias do Estado de São Paulo - Adicionalmente, os resultados desses levantamentos foram integrados ao acervo de informações setoriais do IPT.
- Atividades de campo: entrevistas com representantes de entidades empresariais e com especialistas do setor.
- Diagnóstico qualitativo da indústria cerâmica: embasado na análise e integração das informações coletadas, efetuou-se a caracterização qualitativa da estrutura produtiva e de mercado do parque cerâmico paulista, com ênfase na caracterização das matérias-primas minerais
- Elaboração de cenários: projeção de demanda de minerais industriais cerâmicos para o parque industrial
- Consolidação do diagnóstico técnico-econômico: análise estratégica do setor mínero-cerâmico, destacando-se gargalos, ameaças e oportunidades, e sugestão de políticas e ações para o seu aprimoramento competitivo, sobretudo relacionadas às demandas relativas ao suprimento mineral.
3. Contextualização dos Estudos
Visando subsidiar o entendimento da cadeia produtiva cerâmica, nesse tópico são abordados os principais fatores motivadores dos estudos, classificação da indústria cerâmica, breve histórico de seu desenvolvimento e características gerais dessa indústria no Brasil.
3.1. Fatores motivadores
O setor cerâmico pode ser considerado como uma das primeiras indústrias de transformação implantada no Brasil. Esse seu pioneirismo também é marcante no Estado de São Paulo. Com grande parte de seus produtos suprindo a cadeia de consumo da construção civil, a expansão e modernização da indústria cerâmica participaram diretamente da dinamização da economia e do vigoroso crescimento urbano paulista no Século XX.
A importância setorial fica não só evidente pelo seu relativo realce no relevo da economia estadual, mas também pela sua capilaridade territorial, contando com empreendimentos em parcela significativa dos municípios paulistas. O setor ganha relevância particularmente em algumas regiões, que conta com a concentração de empresas, aonde chega a constituir os chamados arranjos produtivos locais (APLs), ampliando consideravelmente sua inserção na economia desses territórios e sua proeminência na geração de postos de trabalho e renda.
O elevado e diversificado consumo de matérias-primas minerais constitui uma das características peculiares da indústria cerâmica, tendo um peso significativo na matriz de custos das empresas.
Esse dinamismo da indústria cerâmica no Estado tem provocado uma expressiva e crescente demanda de insumos minerais, cujo sistema de suprimento (parte dele situado no Estado), ainda que apresente vários casos com padrão tecnológico satisfatório, padece de aperfeiçoamento em seus processos produtivos e gerenciais, bem como de uma melhor adequação às demais formas de uso e ocupação do solo, e às condições ambientais.
Em função da importância da indústria cerâmica e do seu potencial de expansão, bem como do fato do elo mineral constituir um dos fatores de fragilidade da cadeia produtiva no Estado, o estudo em questão tem como objetivo finalístico subsidiar a elaboração de políticas setoriais dirigidas ao aprimoramento competitivo do parque cerâmico, enfocando-se, em especial, as demandas e possibilidades de melhorias do sistema de suprimento mineral.
3.2. Classificação da indústria cerâmica
A indústria cerâmica compreende uma ampla gama de produtos fabricados por processos e matérias-primas distintas, sendo passível de várias formas de classificação em função de características, entre outras, físico-químicas, composicionais e de aplicação. O Quadro 1 apresenta umas das subdivisões mais usuais, adotada pela Associação Brasileira de Cerâmica – ABC, sendo baseada em critérios técnicos e quanto ao tipo de aplicação 1 .
1 Apesar das indústrias de vidro, cimento e cal envolverem processos e constituírem conceitualmente produtos cerâmicos, por suas particularidades tecnológicas, importância e dimensão do mercado são tratados como setores à parte da indústria cerâmica (www.abceram.org.br).
SETOR CERÂMICO | PRODUTOS |
---|---|
Cerâmica Vermelha ou Estrutural | Materiais empregados na construção civil - tijolos, blocos, telhas, elementos vazados, lajes, tubos cerâmicos e argilas expandidas; e utensílios de uso doméstico e de adorno. |
Revestimentos | Materiais com formato de placas usados na construção civil para revestimento em ambientes internos e externos - paredes, pisos, bancadas e piscinas. Recebem designações tais como: azulejo, pastilha, porcelanato, grês, lajota, piso, etc. |
Cerâmica Branca ▪ Louça sanitária ▪ Louça de mesa ▪ Isoladores elétricos para alta e baixa tensão ▪ Cerâmica artística (decorativa e utilitária) ▪ Cerâmica técnica para fins diversos, tais como: químico, elétrico, térmico e mecânico |
Compreende materiais constituídos tradicionalmente por um corpo branco ou claro e, em geral, recobertos por uma camada vítrea transparente e incolor e que são agrupados pela cor clara da massa, necessária por razões estéticas e/ou técnicas. Com o advento dos vidrados opacificados, muitos dos produtos enquadrados neste grupo passaram a ser fabricados, sem prejuízo das características para uma dada aplicação, com matérias-primas mais impuras, responsáveis pela coloração mais escura do corpo cerâmico. |
Materiais Refratários | Produtos que têm como finalidade suportar temperaturas elevadas nas condições específicas de processo e de operação dos equipamentos industriais, que em geral envolvem esforços mecânicos, ataques químicos, variações bruscas de temperatura e outras solicitações. São classificados com relação quanto às matérias-primas ou ao componente químico principal: sílica, sílico-aluminoso, aluminoso, mulita, cromítico-magnesiano, carbeto de silício, grafita, carbono, zircônia, etc. |
Isolantes Térmicos | Materiais isolantes classificados de acordo com a massa específica e a temperatura de uso: refratários isolantes; isolantes térmicos não refratários, compreendendo produtos como vermiculita expandida, lã de vidro e lã de rocha (empregados até 1.100 ºC); fibras ou lãs cerâmicas que apresentam composições tais como sílica, sílica-alumina, alumina e zircônia, que podem chegar a temperaturas de utilização de 2.000 ºC ou mais. |
Fritas e Corantes | São importantes matérias-primas para diversos segmentos cerâmicos que requerem determinados acabamentos. Frita (ou vidrado fritado) é um vidro moído, fabricado por indústrias especializadas a partir da fusão da mistura de diferentes matérias-primas. Corantes constituem-se de óxidos puros ou misturas de pigmentos inorgânicos sintéticos, sendo utilizados como aditivos aos vidrados e corpos cerâmicos. Esses materiais combinados são aplicados na superfície do corpo cerâmico que, após a queima, adquire aspecto vítreo. Este acabamento tem por finalidade aprimorar a estética, tornar a peça impermeável, aumentar a resistência mecânica e melhorar ou proporcionar outras características específicas. |
Abrasivos | Grãos abrasivos obtidos por processos cerâmicos e produtos obtidos a partir desses materiais, destinados ao trabalho de corte, desbaste retífica e polimento: lixas, rebolos, discos de desgastes e corte, pedra de afiar, etc. |
Cerâmica Avançada | Materiais desenvolvidos a partir de matérias-primas sintéticas de altíssima pureza e por meio de processos rigorosamente controlados. São classificados de acordo com suas funções: eletroeletrônicos, magnéticos, ópticos, químicos, térmicos, mecânicos, biológicos e nucleares. |
Quadro 1. Classificação da indústria cerâmica. Fonte: Associação Brasileira de Cerâmica – ABC (www.abceram.gov.br).
Uma diferenciação importante a ser observada entre as indústrias cerâmicas tradicionais e avançada, diz respeito às suas matérias-primas. Enquanto as primeiras consomem basicamente substâncias minerais naturais, as cerâmicas avançadas são fabricadas a partir de matérias-primas sintéticas de alta pureza, daí as respectivas designações – cerâmica tradicional ou de base silicática e cerâmica avançada ou de óxidos.
De interesse do presente projeto, entre as cerâmicas tradicionais foram priorizados os segmentos industriais 2 de maior relevância econômica no Estado e com consumo significativo de bens minerais, a saber:
- Cerâmica Vermelha
- Revestimentos
- Louça Sanitária
- Louça e Porcelana – Mesa, Utilitários e Decoração
- Colorifícios (Fritas, Esmaltes e Corantes)
- Cerâmica Técnica – Isoladores Elétricos
2 As denominações utilizadas são baseadas na Associação Brasileira de Cerâmica e na literatura internacional e adequadas ao enfoque deste Relatório.
3.3. Histórico e características gerais do setor cerâmico
O setor cerâmico integra o ramo de produtos de minerais não metálicos da Indústria de Transformação, intensivo em capital, sendo que os segmentos mais representativos dessa indústria fazem parte do conjunto de cadeias produtivas que compõem o complexo da Construção Civil.
O desenvolvimento da indústria cerâmica brasileira remonta ao princípio do Século XX, acompanhando as transformações socioeconômicas vivenciadas pelo País, com a intensificação do crescimento urbano e o início do processo de industrialização. A demanda crescente de habitações e obras de infraestrutura mudou o padrão construtivo oriundo do período colonial, forçando a substituição da madeira por tijolos e telhas nas edificações, tanto por razões sanitárias, como pela própria escassez daquela matéria-prima (Silva, 1982). Com o crescimento do consumo de peças cerâmicas, as olarias que operavam de forma familiar e artesanal, tiveram que se adaptar, modernizando as técnicas de produção, com a importação de equipamentos e processos europeus e localizando-se mais perto dos centros urbanos.
O grande avanço do setor cerâmico nacional, no entanto, só foi efetivamente ocorrer a partir de meados da década de 1960, com a implementação de políticas públicas habitacionais, em especial, com a instituição do Sistema Financeiro da Habitação e do Banco Nacional da Habitação. Durante a década de 1970, sustentado por uma demanda continuada, ocorre o “boom” da Construção Civil no País, provocando a expansão da indústria cerâmica nacional.
Na esteira dessa ampliação do setor, deu-se a incorporação de processos inovadores, o lançamento de novas linhas de produtos e, em consequência, o crescimento e a diversificação da produção de minerais industriais para a indústria cerâmica brasileira.
A partir de meados da década passada, a indústria cerâmica passou novamente por um período de franca expansão, motivada pelo crescimento da economia do País e por políticas públicas de fomento ao setor habitacional.
A grande expressão demográfica, em conjunto com a tradição dos processos construtivos, com o uso intensivo de produtos cerâmicos, faz com que a produção dessa indústria no Brasil esteja entre as mais significativas mundialmente.
Com uma produção diversificada, contemplando praticamente todos os segmentos da indústria cerâmica tradicional de base silicática, o Estado de São Paulo concentra parcela importante desse setor industrial brasileiro, sendo que os grandes destaques são os produtos de cerâmica vermelha, revestimentos e sanitários. Conta também com a fabricação de uma gama variada de materiais refratários, de cerâmica branca (louça de mesa, isoladores elétricos, cerâmica artística), isolantes térmicos, e de fritas e corantes.
A despeito da grande capilaridade territorial, como acontece em outras regiões do país, o fator geológico – existência de jazidas -, associado a outros condicionantes favoráveis, como proximidade de mercados, base infraestrutural privilegiada e cultura empresarial, tem conduzido à concentração geográfica do setor cerâmico em territórios específicos, levando à constituição de aglomerados produtivos. Em determinadas regiões, essas aglomerações de empresas chegam a constituir o que se vem conceituando como arranjos produtivos locais (APLs) 3 de base mineral. Nesses casos, as concentrações de empresas podem agregar, no mesmo território, além de cerâmicas e minerações, outros segmentos da cadeia produtiva, como fornecedores de insumos (equipamentos e embalagens) e serviços, apresentando graus variados de interação entre os agentes empresariais e com organismos externos, como governo, associações empresariais, instituições de crédito, ensino e inovação. A experiência tem mostrado que o adensamento da cadeia produtiva de base mineral, associado ao aprendizado e cooperação, entre seus diversos elos e agentes externos, tende a favorecer o incremento da competitividade de todos os negócios associados, com significativos ganhos, sobretudo, ao pequeno e médio empreendedor.
3 O termo arranjo produtivo local, ou simplesmente APL, tem sido utilizado no meio técnico-científico brasileiro e pelos organismos de governo e instituições de apoio ao setor empresarial para referir-se “a concentrações geográficas de empresas e de instituições que se relacionam em torno de um setor ou de uma atividade econômica. Como uma forma de organização espacial da produção, são radicados territorialmente em decorrência das vantagens que a própria localização enseja. Seu diferencial competitivo pode ser potencializado por meio de interações entre os agentes empresariais da cadeia produtiva industrial, contando, geralmente, com a participação de organismos externos – governo, associações empresariais, instituições de crédito, ensino e pesquisa -, o que acarreta economias externas de longo alcance e que tende a beneficiar todos os negócios associados localmente” (Cabral Junior et al., 2010). O setor mínero-cerâmico é uma das cadeias produtivas com tendência à aglomeração geográfica, sendo favorecida por fatores como disponibilidade de matérias-primas, proximidade de mercados e infraestrutura estabelecida.
A Figura 1 ilustra, de forma simplificada, a cadeia produtiva do setor cerâmico diretamente relacionado à construção civil. Articulam-se, à montante da indústria cerâmica, os fornecedores de matérias-primas naturais (indústria extrativa mineral) e sintéticas (colorifícios). No Brasil, enquanto os primeiros caracterizam-se como fornecedores locais, ou, em muitas situações, a própria cerâmica acumula a atividade mineração, os colorifícios incluem grupos internacionais. O mesmo acontece com o fornecimento de equipamentos, que apesar de contar com empresas nacionais, tem participação importante do capital europeu. A jusante da cadeia produtiva tem-se o sistema de distribuição feito por atacadistas, lojas especializadas e “home centers”, em especial no caso de revestimentos e sanitários. Agregam-se ainda, serviços de apoio (pesquisa e inovação, design, financeiro, empresarial, manutenção em geral) e de capacitação e treinamento.
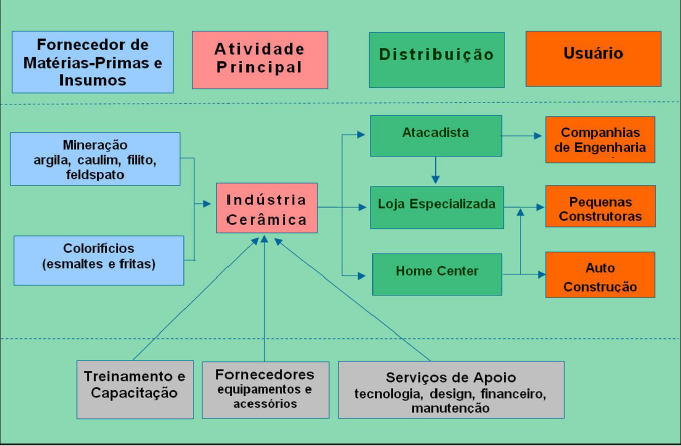
Figura 1. Cadeia produtiva da indústria cerâmica vermelha, de revestimentos e sanitários. Fonte: Cabral Junior e Serra (2006).
A indústria cerâmica é responsável por uma demanda expressiva de insumos minerais, parte deles produzidos no próprio território paulista, que corresponde a uma movimentação anual de cerca de 25 milhões de toneladas de matérias-primas no Estado. A matriz de minerais industriais cerâmicos abarca, entre outras substâncias minerais, argilas de natureza de diversa (argilas comuns, fundentes, plásticas de queima clara e refratárias), caulim, feldspato e rochas feldspáticas, filito, rochas carbonáticas, talco, diopsídio, bentonita, quartzo e zirconita.
O Quadro 2 sintetiza algumas características principais do setor cerâmico no Estado de São Paulo.
- Expressiva concentração industrial – maior parque cerâmico do Brasil, e alguns setores com destaque no cenário mundial (revestimentos, sanitários e cerâmica vermelha).
- Produção diversificada - conta com inúmeros segmentos industriais que fabricam uma grande gama de produtos.
- Demanda derivada da construção civil – grande volume da produção destinado à construção civil.
- Predomínio de micros, pequenas e médias empresas – setorialmente prevalecem amplamente as MPMEs.
- Capilaridade territorial e tendência de constituir aglomerações produtivas – as indústrias são disseminadas territorialmente, sendo comum a sua nucleação em aglomerados produtivos, em função de fatores como proximidade de mercados, disponibilidade de matérias-primas e acesso a infraestrutura.
- Intensiva em recursos minerais – grande consumidora de substâncias minerais: argilas de natureza diversa, caulim, feldspato e rochas feldspáticas, filito, rochas carbonáticas, talco, diopsídio, bentonita, quartzo, zirconita.
- Assimetria empresarial, de mercado e tecnológica – seus segmentos industriais apresentam diferenças com relação à estrutura mercadológica e empresarial, e quanto à maturidade tecnológica.
- Dependência tecnológica - segmentos mais dinâmicos, como o de revestimentos cerâmicos, tem parte importante de seus equipamentos importados.
- Fragilidade do sistema de suprimento mineral – carência de algumas matérias-primas em função do aumento da demanda de setores específicos, tecnologia deficiente de pesquisa, lavra e beneficiamento, o que se reflete na qualidade das matérias-primas, e necessidade de ordenamento territorial da mineração, conciliando-a com as demais formas de uso e ocupação do solo e com as limitações ambientais, de forma a propiciar a disponibilidade sustentável de substâncias minerais.
Quadro 2. Características da estrutura produtiva e de mercado da indústria cerâmica no Estado de São Paulo.
4. Indústria Cerâmica no Estado de São Paulo
A estimativa do dimensionamento do parque industrial cerâmico no Estado foi efetuada a partir da base de dados da Relação Anual de Informações Sociais do Ministério do Trabalho e Emprego - RAIS/MTE, da qual são extraídas as informações de empregos e estabelecimentos. Apesar das limitações dessas informações 4 , trata-se do único banco de dados de relativa consistência, que contempla toda a indústria cerâmica, sendo passível de desagregação em subclasses, com correspondência nos principais segmentos cerâmicos aqui analisados. Esses dados especializados permitem visualizar a distribuição dessa indústria, bem como indicar os principais polos produtores cerâmicos no Estado. A Figura 2 ilustra a dinâmica econômica da indústria cerâmica entre 2011 e 2016.
4 As informações constantes da base RAIS/MTE são autodeclaradas pelo empreendedor, sendo passíveis de enganos com relação ao enquadramento da sua atividade na classificação CNAE (Cadastro Nacional da Atividade Econômica do IBGE), e abrange exclusivamente as empresas formalizadas, sendo comum microempresas informais (olarias) operando no Estado.
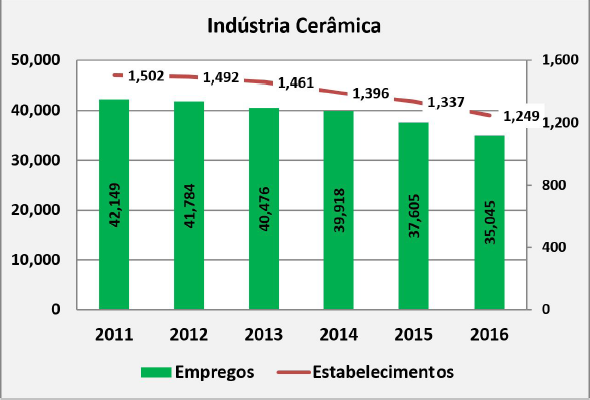
Figura 2. Evolução do número de estabelecimentos e empregos da indústria cerâmica no Estado de São Paulo – 2011 a 2016. Fonte: baseado em RAIS - MTE (2018).
No período de 2011 e 2016 é bastante nítida a queda do número de empregos e de estabelecimentos, que decresceram conjuntamente em 17%, fazendo com que nesses anos mais recentes o parque cerâmico paulista esteja operando em um patamar com 1.250 empresas e 35.000 empregos.
A diminuição desses indicadores é consequência basicamente de dois fatores econômicos. Um primeiro aspecto a se observar é que de fato houve uma retração dessa indústria frente à perda do dinamismo da economia brasileira, sobretudo da construção civil, o que ocorreu notadamente a partir de 2014. Soma-se a isto, uma tendência importante que vem ocorrendo desde o início dos anos 2000, relacionada à concentração dessa indústria, particularmente do setor de cerâmica vermelha, com o fechamento paulatino de micro e pequenas empresas, e a centralização da produção em empresas mais competitivas - geralmente maiores, com maior grau de mecanização e empresarialmente mais estruturadas.
5. Indústria de Cerâmica Vermelha
O segmento de cerâmica vermelha tem como atividade a produção de elementos estruturais, de vedação e de acabamento para a construção civil, como blocos, telhas, tijolos maciços, lajotas e tubos, além de produtos para fins diversos como argilas piroexpandidas, objetos ornamentais e utensílios domésticos.
5.1. Estrutura produtiva e empresarial
5.1.1. Panorama brasileiro
No contexto nacional, a indústria de cerâmica vermelha responde por um faturamento em torno de R$ 18,0 bilhões/ano, segundo dados da Anicer – Associação Nacional da Indústria Cerâmica 5 . Segundo dados da RAIS - MTE (2018), o setor contava com 5.532 estabelecimentos em 2016, empregando um contingente de 87.280 profissionais, constituindo um dos maiores parques de produção de cerâmica vermelha no mundo.
5 Registra-se que o faturamento anual da produção brasileira estimado pela Anicer permanece o mesmo desde 2010, carecendo de atualização e consolidação mais acurada.
Essa indústria é abastecida por um grande número de unidades produtivas de argilas comuns distribuídas em todos os estados brasileiros, caracterizada, na sua grande maioria, por micro e pequenas empresas, geralmente de estrutura familiar. Esse mesmo tipo de matéria-prima é consumido por outros setores, tais como: cerâmica de revestimento de base seca, cimenteiro, agregado leve, entre outros.
A indústria de cerâmica vermelha no Brasil, e o mesmo pode ser reportado ao Estado de São Paulo, caracteriza-se como um segmento econômico expressivo e de grande pulverização territorial. Raramente depara-se com um município ou uma região que não tenha uma cerâmica ou um núcleo de pequenas olarias. Nas proximidades das unidades industriais, juntam-se as lavras de argila, pertencentes aos próprios ceramistas e a pequenos mineradores.
Trata-se de um setor com uma estrutura empresarial bastante assimétrica, pulverizada e de capital estritamente nacional, no qual coexistem pequenos empreendimentos familiares artesanais (olarias, em parte não incorporadas nas estatísticas oficiais), cerâmicas de pequeno e médio porte, com deficiências de mecanização e gestão, e empreendimentos de médio a grande porte (em escala de produção) de tecnologia mais avançada (processos mais automatizados, com preparação melhor da matéria-prima, secagem forçada e fornos de queima semicontínua ou contínua).
5.1.2. Cenário paulista
Como no contexto nacional, a cerâmica vermelha constitui o segmento industrial mais expressivo do setor cerâmico paulista, o que pode ser visualizado na Figura 3.
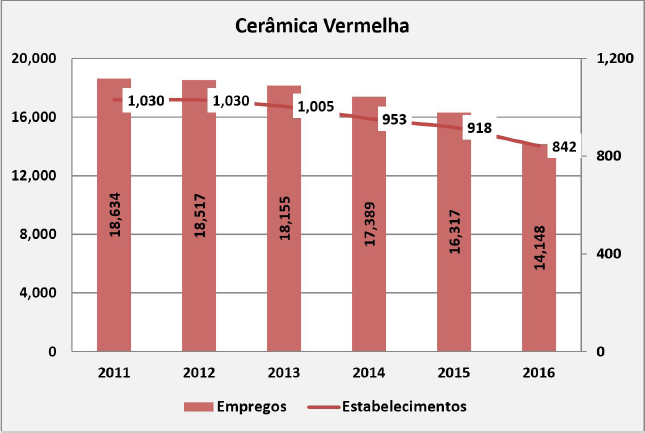
Figura 3. Evolução do número de estabelecimentos e empregos da indústria de cerâmica vermelha no Estado de São Paulo – 2011 a 2016. Fonte: baseado em RAIS - MTE (2018).
Em 2016, a indústria de cerâmica vermelha contava com 842 estabelecimentos e 14.148 postos de trabalho, o que representava 67,4% e 40,4%, respectivamente, do total de empresas e empregos gerados pelo setor cerâmico no Estado.
Enquanto a diminuição do número de estabelecimentos foi de 18,2% no período de 2011 a 2016, acompanhando aproximadamente a tendência setorial, a queda do número de empregos foi mais acentuada, com 24%. Como já mencionado, além do arrefecimento econômico, a indústria de cerâmica vermelha passa por um processo de concentração industrial, o que já ocorreu no século passado em países de tradição cerâmica, como Itália, Espanha e Portugal.
O Estado de São Paulo abriga o maior parque industrial do setor no país, que se concentra em cerca de 15 aglomerações produtivas, parte delas reconhecida pelas instâncias governamentais como arranjos produtivos locais - APLs de Itu, Tatuí, Tambaú, Vargem Grande do Sul e Panorama (conhecido também como APL de cerâmica vermelha do Oeste Paulista), como ilustra a Figura 4.
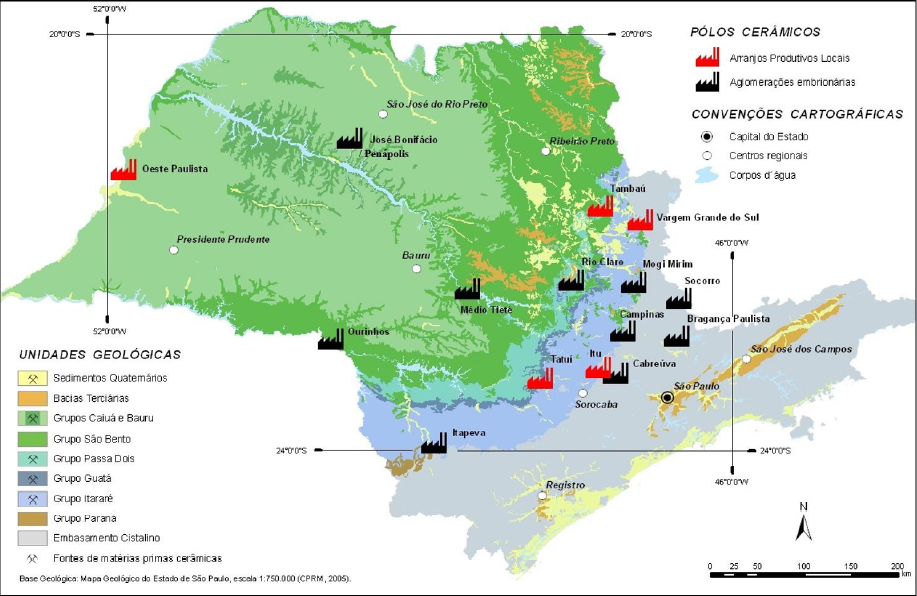
Figura 4. Polos de cerâmica vermelha do Estado de São Paulo. Fonte: adaptado de Cabral Junior et al. (2012).
Dispondo de uma produção diversificada, suas cerâmicas atendem essencialmente o mercado paulista, e, em menor escala, outros estados da federação, havendo registros de exportações pontuais para alguns países da América Latina e os Estados Unidos. Pelas informações disponíveis, pode-se inferir que a produção paulista situa-se em um patamar anual de cerca de 6 bilhões de peças, o que corresponde a 12 milhões de toneladas de cerâmicas queimadas e ao consumo anual de 14,5 a 15,0 milhões de toneladas de matéria-prima (argilas comuns). As bases para essa estimativa constam da Tabela 1.
Peças | Toneladas (2 kg/peça) |
Consumo de Argila (t) Relação Argila/Peça: 1,2/1 |
|
---|---|---|---|
Unidade Fabril Produção Anual Média |
7.200.000 | 14.400 | 17.280 |
Produção do ESP - 842 empresas | 6.062.400.000 | 12.124.800 | 14.549.760 |
Tabela 1. Estimativas de produção de peças e consumo de argila na indústria de cerâmica vermelha.
A distribuição das aglomerações de cerâmica estrutural guarda íntima relação com os terrenos geológicos portadores das principais jazidas de argila. Em primeiro plano, distingue-se uma sequência de polos que acompanha a Depressão Periférica Paulista, associando-se às minerações que exploram a extensa faixa de afloramentos de rochas pelíticas permocarboníferas da Bacia Sedimentar do Paraná. Constituem uma faixa que se estende do sul do Estado (região de Itapeva) até a porção nordeste (região de Tambaú), praticamente contínua, e com regiões em que a aproximação das concentrações industriais chega a formar um amalgamento de aglomerações.
Levantamentos sobre produção e consumo de argilas para fins cerâmicos em outros países, analisados comparativamente com os dados estaduais, sugerem que este conjunto sequencial de aglomerações reúne a mais expressiva concentração de empresas de cerâmica vermelha das Américas, configurando o que pode ser designado de Cinturão Mínero-Cerâmico Paulista. Os outros polos mínero-cerâmicos do Estado distribuem-se de maneira isolada, com as principais aglomerações situando-se no Oeste Paulista, associadas às faixas lindeiras dos principais rios (Paraná, Tietê e Paranapanema), de onde provém o suprimento mineral.
Fatores estruturais têm contribuído com a dinamização da indústria de cerâmica vermelha, incluindo a criação da Anicer há cerca de 30 anos, que tem promovido várias ações para o aprimoramento competitivo do setor, o surgimento de uma rede de laboratórios capitaneados pelo Serviço Nacional da Indústria – SENAI, a inserção do setor em programas voltados para a normalização, como o Programa Brasileiro da Qualidade nas Habitações – PBQP-H, e o envolvimento crescente do meio acadêmico, em trabalhos de pesquisa e desenvolvimento tecnológico, voltados para a área de cerâmica vermelha, como o desenvolvimento do uso de novos combustíveis, estudos de incorporação de resíduos na massa cerâmica e diversificação da produção.
5.2. Processo produtivo
O setor de cerâmica vermelha utiliza a chamada massa monocomponente 6, composta, basicamente, só por argilas, isto é, não envolve a mistura de outras substâncias minerais (caulim, filito, rochas feldspáticas, talco e rochas calcárias), como em outros segmentos da indústria cerâmica, casos das louças de mesa e sanitários.
6 Massa simples ou monocomponente: refere-se à massa formada por uma só matéria-prima, que encerra as necessárias proporções entre os minerais, que permitam a manufatura da peça cerâmica desejada. Podem ser relacionadas, por exemplo, as massas para o fabrico de telhas, tijolos e revestimentos da via-seca. Tratam-se das massas constituídas somente de materiais argilosos, podendo conter, às vezes, a mistura de mais de um tipo de argila, ou de materiais argilo-arenosos. Massa composta: é denominada quando ocorre mistura de diversas matérias-primas na massa. Tratam-se, por exemplo, das massas triaxiais de porcelana e das massas de louça sanitária e de revestimentos via-úmida.
A formulação da massa é feita geralmente de forma empírica pelo ceramista, envolvendo a mistura de uma argila “gorda”, caracterizada pela alta plasticidade, granulometria fina e composição essencialmente de argilominerais, com uma argila “magra”, rica em quartzo e menos plástica, que pode ser caracterizada como um material redutor de plasticidade e que permite a drenagem adequada das peças nos processos de secagem e queima.
Busca-se por meio da composição dessa mistura, a composição de uma massa que tenha algumas funções tecnológicas essenciais, tais como:
- Plasticidade: propiciar a moldagem das peças.
- Resistência mecânica à massa verde e crua: conferir coesão e solidez às peças moldadas, permitindo a sua trabalhabilidade na fase pré-queima.
- Fusibilidade: favorecer a sinterização e, consequentemente, a resistência mecânica e a diminuição da porosidade.
- Drenagem: facilitar a retirada de água e a passagem de gases durante a secagem e queima, evitando trincas e dando rapidez ao processo.
- Coloração das peças: atribuir cores às cerâmicas por meio da presença de corantes naturais (óxidos de ferro e manganês).
No processo de fabricação, a massa é umidificada acima do limite de plasticidade (geralmente entre 25 a 30% de umidade), e processada em misturadores e homogeneizadores, sendo conformadas a seguir em extrusoras (marombas), quando adquirem as suas formas finais (blocos, lajes, lajotas, tubos) ou seguem para prensagem (telhas) ou tornearia (vasos).
Quanto aos processos de secagem, o nível de sofisticação é bastante diferenciado entre as diversas unidades industriais. Naquelas de menor porte, ainda é relativamente comum a prática de secagem natural, arranjando os materiais em pilhas expostas ao tempo ou em galpões cobertos, em alguns casos dispostas sobre as paredes aquecidas dos fornos. Secadores do tipo estufas estáticos ou semicontínuos geralmente são utilizados em empresas mais estruturadas, de médio e grande porte, onde se aproveita o calor recuperado dos fornos durante os períodos de resfriamento da carga.
Com exceção de algumas unidades fabris mais modernas e automatizadas, que utilizam fornos contínuos na fase de queima, a grande maioria empregada é de construção rústica, do tipo intermitente, com paredes construídas em alvenaria de tijolos comuns, de formatos circulares e tetos em forma de abóbadas (“fornos abóbadas”), e fornos retangulares (“fornos paulistinhas”), bastantes típicos. Na geometria, dimensões e capacidades das câmaras apresentam variações, com predominância das câmaras circulares para a produção de telhas, tradicionalmente consideradas como mais adequadas à fabricação desses produtos. 7 Conta-se também, em menor número, com fornos de alimentação semicontínua do tipo Hoffman, de maior produtividade. A Figura 4 ilustra o fluxograma dos processos de fabricação de blocos e telhas.
7 Mais recentemente, outra concepção de forno intermitente introduzido em alguns polos cerâmicos é o tipo vagão. O equipamento é constituído por uma câmara em forma de vagão, que se desloca sobre as cargas - enquanto a câmara está queimando, outra carga está sendo montado ou no processo de resfriamento. Além do ganho de produtividade em relação aos fornos intermitentes tradicionais, sua operação propicia melhores condições de trabalho aos funcionários.
Processo diferente é utilizado na obtenção de agregado leve cerâmico, em que o material argiloso – com teores adequados de fundentes (álcalis) e de substâncias formadoras de gases (hidróxidos de ferro, matéria orgânica e carbonatos) – é queimado em fornos rotativos, com altas temperaturas (1.100 a 1.200 ºC), propiciando a formação de grande quantidade de fase vítrea, que retém os gases gerados na queima, provocando a expansão do material cerâmico.
Com exceção do agregado leve, a maioria dos produtos de cerâmica vermelha apresenta alta porosidade aberta, com pouca fase vítrea, decorrente da baixa temperatura de queima (800 a 950 ºC). Mesmo assim, possuem resistência mecânica suficiente para os usos a que são destinados. Nesses casos, os fundentes presentes estão contidos nas estruturas das argilas ilíticas e esmectíticas presentes ou adsorvidas nas caulinitas, tais como complexos ferruginosos e sais solúveis, que reagem durante os longos períodos de queima.
A exigência técnica dos produtos de cerâmica vermelha é mais rigorosa para telhas e blocos estruturais, requerendo maior sinterização das peças. Nesses materiais, as argilas devem ser mais ilíticas ou conter a mistura destas ou de outros fundentes como filitos, como já vem sendo experimentado em algumas regiões do país (por exemplo, Monte Carmelo-MG).
Prevalece amplamente no setor o uso de biomassa como combustível. Até o início dos anos 2000, o uso de lenha em toras (preponderantemente eucalipto) para queima direta nos fornos era generalizado nos diversos polos produtores. De forma mais restrita, esta prática ainda se observa, principalmente em alguns polos oleiros. Atualmente, o mais comum é a trituração de lenha e a utilização de resíduos, como os da indústria de processamento de madeira (serrarias, indústria de móveis, etc.), para a produção de fragmentos como cavacos, “chips” e serragem. Esses materiais são alimentados nas fornalhas por dispositivos mecânicos (silos e roscas transportadoras) geralmente dotadas de certa automatização no controle de vazão do combustível.
As vantagens do uso de cavacos e serragem são bastante notáveis tanto na redução do consumo equivalente de energia, cerca de 5% menor em relação à operação com lenha em toras, como o de possibilitar reduções da ordem de 20% no tempo dispendido no processo de queima, com impactos positivos na produtividade (IPT, 2007). O nível de organização do processo produtivo é bastante diferenciado entre as empresas, observando-se de modo generalizado, que é maior e mais sofisticado com o porte da indústria.
Em algumas indústrias de maior porte, com processos mais automatizados, são utilizados fornos de alimentação contínua, do tipo túnel. Nestes, as peças são empilhadas sobre vagonetas que percorrem o forno num único sentido. Com este tipo de forno são eliminadas as interrupções de queima para cada carga e descarga, aumentando significativamente a produção pela redução do tempo de queima, e diminui-se a heterogeneidade vertical da temperatura dentro dos fornos, o que propicia produtos com qualidade mais homogênea.
Já se sabe que a maior uniformidade da qualidade do produto, tanto no aspecto visual quanto no atendimento aos requisitos das normas de desempenho, pode ser obtida empregando-se processos contínuos de queima em fornos com regime de operação contínua (forno tipo túnel). Nas experiências de utilização de fornos túneis convencionais do tipo vagonetas, operando com gás natural - GN ou GLP para queima de telhas ou blocos, constatou-se que há menor consumo específico de energia e padrões mais uniformes de qualidade. No entanto, o uso de forno túneis com esses combustíveis ainda não são competitivos se considerados a diferença de custo operacional e de investimento inicial existente entre estes e os fornos intermitentes e semicontínuos (IPT, 2007). Para a minimização de custos, a solução encontrada por algumas cerâmicas dotadas de forno túnel é a produção de peças de maior valor agregado (tais como, blocos estruturais e telhas) e o uso de madeira pulverizada ou mesmo a combinações de combustíveis, como carvão mineral, GN e óleo combustível.
5.3. Sistema de suprimento mineral
5.3.1. Características das matérias-primas: contexto geológico e características tecnológicas
As matérias-primas empregadas na indústria de cerâmica vermelha correspondem às denominadas argilas comuns (common clays), que abrangem uma grande variedade de substâncias minerais de natureza argilosa. Compreendem, basicamente, sedimentos pelíticos consolidados e inconsolidados, como argilas aluvionares quaternárias, argilitos, siltitos, folhelhos e ritmitos, que queimam em cores avermelhadas, a temperaturas variáveis entre 800 °C e 1.250 °C (Cabral Junior et al., 2009).
Essas argilas possuem granulometria muito fina, característica que lhes conferem, com a matéria orgânica incorporada, diferentes graus de plasticidade, quando adicionada de determinadas porcentagens de água, além da trabalhabilidade e resistência mecânica a seco e após o processo de queima. Tais aspectos são importantes para a fabricação de uma grande variedade de produtos cerâmicos. As cores de queima tipicamente avermelhadas são decorrentes do elevado conteúdo de óxido de ferro desses materiais, que se tornam mais proeminentes a partir de teores superiores a 4% (Facincani, 1992).
Segundo a subdivisão tipológica proposta por Motta et al. (2004), de acordo com o contexto geológico, as concentrações econômicas de argilas para cerâmica vermelha e revestimentos no Estado podem ser individualizadas em dois grandes grupos tipológicos: argilas formacionais e argilas quaternárias (Quadro 3).
TIPO | GÊNESE | CARACTERÍSTICAS DOS DEPÓSITOS | MATÉRIAS-PRIMAS | ||
CONTEXTO GEOLÓGICO | FORMA E DIMENSÃO | COMPOSIÇÃO | PROPRIEDADES CERÂMICAS | ||
Quaternário | Sedimentar Detrítico | ▪ Depósitos de preenchimento de fundo de vales, associado às áreas de transbordamento das planícies aluviais atuais (várzeas e canais abandonados) e em terraços sobrelevados (paleoplanícies) ▪ Pequenas depressões lacustres continentais ▪ Planície costeira, associado a áreas de inundação, com aporte sedimentar fluvial e, eventualmente, com alguma influência marinha ▪ Idade – depósitos recentes a pliopleistocêncios |
▪ Forma: bolsões lenticulares ▪ Espessura: 1 a 8 m ▪ Reservas Geológicas: porte variável – 0,02 a 5 milhões de m³ |
▪ Argilas inconsolidadas com contribuição variável de silte e areia (70 a 90% < 325 #) ▪ Fração argila: composta de caulinita, com teores variáveis de illita e esmectita ▪ Teor de álcalis: 1 a 2% ▪ Teor de ferro: 4 a 8% ▪ Matéria orgânica: conteúdo apreciável |
▪ Elevada plasticidade facilita a extrusão das peças ▪ Relativa refratariedade e conteúdo de matéria orgânica tendem a limitar o emprego em produtos que exigem maior resistência mecânica e baixa absorção de água |
Formacional | Sedimentar e Alteração Intempérica | ▪ Rochas pelíticas associadas a bacias sedimentares terciárias a paleozóicas, correspondendo a sedimentos depositados em amplos ambientes marinhos (costeiros e plataformais) e lacustres. ▪ Camadas mais superficiais sujeitas à alteração intempérica (lixiviação de álcalis e caulinização) ▪ Ocorrências em níveis planálticos diversos, na forma de colinas, morrotes e tabuleiros |
▪ Forma: Tabular ▪ Espessura: 4 a 20 m ▪ Reservas Geológicas: grande porte – milhões a dezenas de milhões de m³ |
▪ Taguás - rochas pelíticas fundentes com alteração variável: argilitos, ritmitos, siltitos e folhelhos (mais de 80%< 325 #) ▪ Fração argila: predominância de illita, com contribuição de esmectita e camadas mistas (I-E); conteúdo de caulinita aumentando com o grau de alteração das rochas ▪ Teor de álcalis: 2 a 7% ▪ Teor de ferro: 5 a 10% ▪ Matéria orgânica: ausente ou em pequenas proporções |
▪ Granulometria fina e teores elevados de óxidos fundentes propiciam elevada resistência mecânica e baixa absorção de água |
Quadro 3. Características dos depósitos de argila para cerâmica vermelha.
Fonte: Extraído de Cabral Junior et al. (2012).
5.3.1.1. Depósitos de argilas formacionais
Os depósitos formacionais, também denominados de argilas de bacias sedimentares, no território paulista estão inseridos na borda leste da Bacia do Paraná. Seus conjuntos pelíticos intensamente lavrados e que abastecem os cinco polos cerâmicos situados na Depressão Periférica Paulista – entre outros, de Tatuí, Itu, Rio Claro, Tambaú e Vargem Grande do Sul (ver Figura 5) fazem parte da Sequência Permocarbonífera, mais especificamente do Grupo Itararé (indiviso em São Paulo), Grupo Guatá (Formação Tatuí), e Grupo Passa Dois (em especial, a Formação Corumbataí).
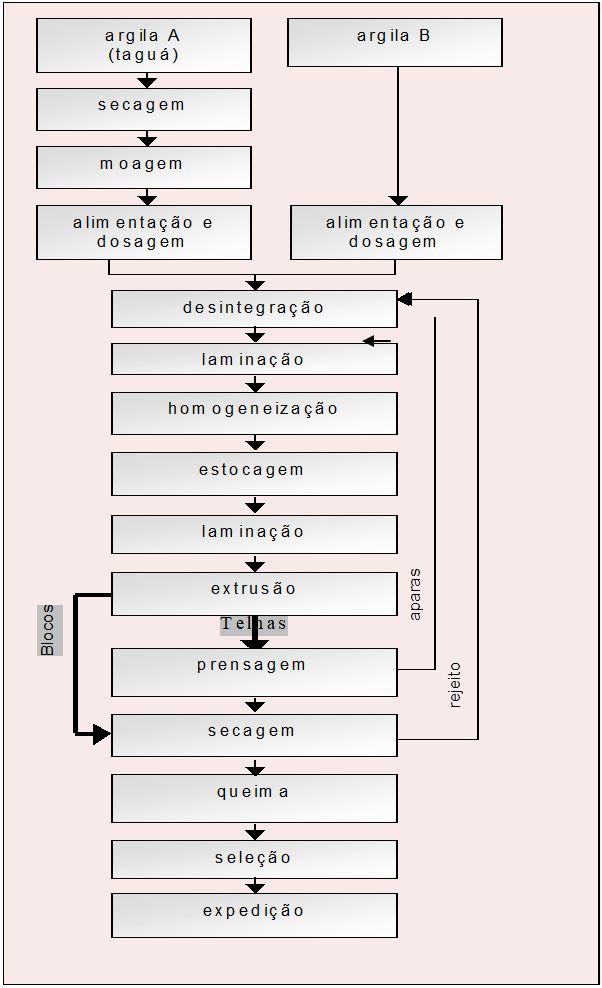
Figura 5. Fluxograma dos processos de fabricação de blocos e telhas. (Modificado de São Paulo, 1992).
Característica importante das argilas formacionais é a grande dimensão dos seus depósitos. 8 As rochas de interesse cerâmico são os folhelhos, argilitos, siltitos, ritmitos e outras rochas de natureza pelítica, que são denominadas genericamente de “taguás” no jargão cerâmico. Os taguás possuem granulometria fina, geralmente como argilitos sílticos ou siltitos argilosos, com mais de 80% das partículas menores que 325 mesh e 40 a 60% do material contido na fração argila (menor que 0,004 mm).
8 As unidades sedimentares citadas foram depositadas em extensos ambientes marinhos costeiros e plataformais em determinados períodos evolutivos, e que acomodaram camadas de rochas pelíticas espessas e contínuas, com relativa homogeneidade textural, que podem atingir espessuras de algumas dezenas de metros. Configuram-se assim como depósitos com grandes reservas explotáveis, comumente envolvendo dezenas de milhões de toneladas.
A composição dos argilominerais inclui principalmente ilita, associada a proporções variáveis de esmectita, camadas mistas (I-E) e caulinita. Enquanto a presença dos três primeiros está vinculada aos processos de sedimentação e diagênese do pacote pelítico, a participação significativa da caulinita está relacionada à ação de processos intempéricos lixiviantes, formando-se a partir da degradação da ilita, esmectita e de feldspato detrítico.
A granulometria fina e o elevado teor de álcalis, associado sobretudo ao conteúdo potássico das ilitas contido nas rochas frescas ou pouco intemperizadas, proporcionam aos taguás desempenho cerâmico destacado, apresentando resistência mecânica elevada e baixa absorção de água após queima em temperaturas na faixa de 800 °C a 1.150 °C. Já a alteração intempérica dos horizontes mais superficiais, que provoca a remoção parcial dos óxidos fundentes e o incremento da refratariedade, propicia a desagregação dos materiais, diminuição da granulometria e aumento da plasticidade, o que facilita o processo de conformação das massas cerâmicas e incrementa as reações de sinterização durante a queima das peças.
A partir desse tipo de matéria-prima, as indústrias do Cinturão Cerâmico Paulista preparam uma série de massas, por meio de misturas entre diferentes rochas pelíticas, menos e mais alteradas, que suprem uma produção diversificada, desde blocos cerâmicos até tubos, revestimentos e agregado leve. Eventualmente em situações mais restritas, as misturas podem incluir também argilas aluviais quaternárias, principalmente quando se deseja incrementar a plasticidade das massas.
5.3.1.2. Depósitos de argilas quaternárias
Os quatro polos que centralizam a produção de cerâmica vermelha na região oeste do Estado – Barra Bonita, Ourinhos, Penápolis e Panorama-Pauliceia, são supridos por argilas lavradas a partir de jazidas de idade Quaternária (Figura 4).
Trata-se de acumulações sedimentares de fundo de vales, associados a planícies atuais e terraços aluvionares (paleoplanícies), ocorrendo, mais restritamente, em pequenas bacias lacustres. Nesses locais, formam-se depósitos de formato lenticular, com espessuras de porte métrico, que ocupam áreas de poucos hectares até alguns quilômetros quadrados, comumente intercalados a lentes e camadas arenosas.
As jazidas são formadas por sedimentos argilosos inconsolidados, constituídos essencialmente de caulinitas detríticas, e, em menor proporção, de quantidades variáveis de quartzo. De forma subordinada, pode incorporar também outros argilominerais (illita e esmectita), além de conteúdo de muscovita, feldspatos, óxidos e hidróxidos de ferro, o que lhes conferem a característica de queima avermelhada.
De forma geral, os depósitos de argila quaternária são texturalmente mais heterogêneas que os formacionais, possuindo de 70 a 95% de partículas menores que 325 mesh em média. A matéria orgânica geralmente contida nessas argilas inconsolidadas incrementa a sua plasticidade, facilitando o processo de moldagem dos produtos cerâmicos. Colabora também no aumento da resistência mecânica das peças secas, possibilitando manuseio adequado durante o processo de fabricação dos produtos.
No entanto, a composição essencialmente caulinítica e o baixo teor de álcalis são responsáveis pela relativa refratariedade desses materiais argilosos. Isto tende a destiná-los à fabricação de produtos menos exigentes quanto aos parâmetros de resistência e absorção de água. Consequentemente, essas propriedades cerâmicas influenciam na produção dos polos do oeste paulista, especializados na confecção de blocos de vedação e lajes.
As massas cerâmicas empregadas nos polos do oeste paulista são preparadas empiricamente, envolvendo a mistura de uma argila “gorda”, caracterizada pela alta plasticidade, granulometria fina e composição essencialmente de argilominerais, com uma argila “magra”, rica em quartzo e menos plástica, que pode ser caracterizada como um material redutor de plasticidade e que permite a drenagem adequada das peças nos processos de secagem e queima.
5.3.2 Mineração de argila
5.3.2.1. Estrutura de mercado e tecnologia mineral
A mineração de argila constitui uma atividade econômica atrelada localmente à sua indústria de transformação. A produção ocorre quase sempre de forma cativa (as minas pertencem aos próprios ceramistas), havendo, frequentemente, comercialização de excedentes de argila. 9
9 Por se tratar de substâncias minerais de baixo valor econômico, as matérias-primas para cerâmica vermelha não comportam transporte a grandes distâncias, condicionando a instalação das cerâmicas o mais próximo possível das jazidas.
Predominam empreendimentos de pequeno a médio porte, com produções variando de 5.000 a 40.000 t/mês, em lavras com escavações mecânicas a céu aberto. De modo geral, as minas carecem de investimentos em modernizações tecnológicas e gerenciais necessárias ao aprimoramento do sistema de produção (pesquisa mineral, lavra e beneficiamento), sendo praticamente inexistentes programas de certificações quanto à qualidade e gestão ambiental.
Os dados oficiais apontam para a existência de pelo menos 234 minas de argila comum em operação no Estado (Tabela 2). 10 Os preços praticados pelo mercado estão na faixa de R$ 5,00 a R$ 20,00/t (FOB), comercializada in natura, dependendo da disponibilidade local, da qualidade da matéria-prima e da finalidade de uso.
10 Os dados do DNPM computam de forma agregada as minas que abastecem o mercado de cerâmica vermelha, e aquelas que suprem as fábricas de revestimentos cerâmicos via seca, centralizadas no Polo de Santa Gertrudes, que empregam como matéria-prima argilas comuns de origem formacional (Formação Corumbataí).
Porte | Grande | Média | Pequena | Micro | Estado de São Paulo |
---|---|---|---|---|---|
Minas | 2 | 30 | 100 | 102 | 234 |
Classificação das empresas de acordo com a produção anual bruta (ROM): Grande maior 1.000.000 t / Média: entre 100.000 e 1.000.000 t / Pequena: entre 10.000 e 100.000 t / Micro: abaixo de 10.000 t. Fonte: DNPM (2016). |
Tabela 2. Minas de argila comum no Estado de São Paulo - ano base 2014.
A mineração de argila carece de profissionais qualificados para a condução das operações da mina e para caracterização e controle das matérias-primas. Essa deficiência de capacitação da mão de obra associada à incipiente tecnologia empregada (equipamentos e processos) reflete-se em carências de padronização e de qualidade das matérias-primas, com consequentes prejuízos na produção cerâmica.
As operações mineiras praticamente restringem-se à extração de argilas, com as matérias-primas sendo comercializadas in natura, com o carregamento e expedição feitos diretamente na frente de lavra ou a partir de pilhas de estocagem. Geralmente, os processos de homogeneização, sazonamento e composição de misturas de matérias-primas são realizados no pátio das cerâmicas. Eventualmente, algumas mineradoras podem agregar etapa de beneficiamento como secagem, homogeneização e cominuição de argilas. Isto ocorre em APLs mais estruturados, aonde já vem tendo a participação mais efetiva de empreendedores especializados, como mineradores e fornecedores de argila. Trata-se de uma tendência recente, sendo que se inicia também um processo, ainda incipiente, de lavras cooperativadas de ceramistas - “mineradoras comuns” (p.ex. Panorama-Pauliceia – SP).
Nas minerações mais bem estruturadas, as operações de lavra costumam ser condicionadas a fatores como: situação topográfica do depósito, distribuição espacial das camadas de argila, características físicas do material, escala de produção, nível de investimento necessário e tipos de cuidados ambientais. As categorias de equipamentos mais utilizados são (Cabral Junior et al., 2009):
- Depósitos minerais localizados nas encostas dos morros (jazidas de bacias sedimentares): são lavrados principalmente por escavadeiras hidráulicas sobre esteiras e, em alguns casos, por carregadeiras sobre rodas, podendo ainda ser auxiliadas por carregadeiras de esteiras e tratores sobre rodas. Estes equipamentos são amplamente empregados para produções de pequeno a médio porte.
- Depósitos minerais formados por camadas horizontais de pequena profundidade em subsuperfície (jazidas de argilas quaternárias): são lavrados por escavadeiras hidráulicas e podem contar com carregadeiras nos serviços de apoio, nas produções de pequeno a médio porte. O avanço das lavras em encosta ou com aprofundamento em cava pode atingir desníveis de escavação de até 20 m. Na maior parte das minerações, as máquinas que realizam a escavação mecânica também são responsáveis pela operação de carregamento das unidades de transporte do material escavado. No transporte, são usualmente empregados caminhões basculantes convencionais. 11
11 Há situações em que o minério e seu capeamento apresentam-se compactados (a exemplo dos argilitos e siltitos, conhecidos regionalmente como taguás) para escavação direta. Nestes casos, pode ser necessário o desmonte com explosivos para fragmentar o material e, em seguida, proceder o seu carregamento e transporte.
A Figura 6 apresenta o fluxograma simplificado das operações unitárias da produção de argila e preparação de massa, envolvendo o sistema mina-cerâmica.
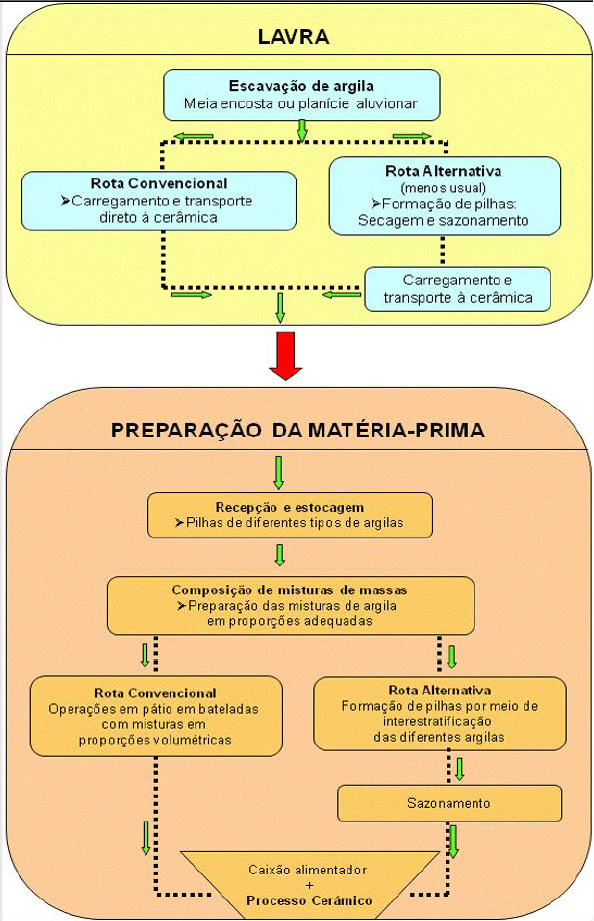
Figura 6. Fluxograma das operações unitárias da produção de argila e preparação de massa cerâmica. Fonte: Cabral Junior et al. (2009).
A necessidade de se obter peças de características uniformes, dentro de especificações normatizadas, seja para a obtenção de produtos com qualidade reconhecida no mercado, seja para a certificação, impõe o controle de qualidade como parte fundamental do processo produtivo industrial.
Para tanto, os controles de processo devem obrigatoriamente ser iniciados pela garantia da qualidade e constância das propriedades das matérias-primas, o que depende do conhecimento das jazidas, antes mesmo da extração das argilas, e continua nas etapas subsequentes do processo fabril. De uma maneira geral, os jazimentos minerais são únicos e, portanto, para cada depósito deve ser buscado um projeto específico de lavra, adequado às características locais quantitativas e qualitativas dos minérios argilosos.
5.3.2.2. Aspectos ambientais da mineração de argila
Na mineração de argila constata-se pouca geração de resíduos resultantes, geralmente, da remoção do capeamento superficial (solo) e, mais subordinamente, da retirada de camadas estéreis intercaladas ao pacote de minério argiloso. O volume de resíduos gerado está condicionado às relações de mineração (estéril/minério). Em decorrência do baixo valor do minério argiloso, são lavradas jazidas com baixa relação estéril/minério, geralmente com valores inferiores 0,25, isto é, para cada tonelada de argila são removidos menos de 0,25 tonelada de materiais estéreis.
Os materiais descartados na frente de lavra são constituídos por sedimentos de natureza mais ou menos arenosa. Quando utilizados, destinam-se à pavimentação de acessos internos na mina e ao reafeiçoamento do relevo das áreas impactadas pela mineração, em trabalhos de estabilização e preenchimentos de cavas já lavradas. Materiais arenosos mais puros podem, eventualmente, ser aproveitados como agregado miúdo na construção (argamassas e concreto) e fins industriais (fundição), como ocorre, por exemplo, em mina de cerâmica na região de Itu no Estado de São Paulo. Nesta mina, onde são mineradas rochas da Bacia do Paraná, parte dos sedimentos não aproveitados pela cerâmica, é beneficiado para purificação da fração arenosa (hidrociclonagem) e comercializados como coproduto da jazida.
A mineração de argila por ser praticada em empreendimentos de pequeno porte e envolver, basicamente, processos de remoção de materiais sólidos provoca, de forma geral, impactos ambientais restritos.
As práticas mais comuns utilizadas no controle das áreas impactadas pela mineração envolvem medidas de mitigação convencionais, a saber:
- Restrição da remoção da vegetação ao mínimo necessário e revegetação das áreas impactadas, sempre que possível.
- Instalação de sistema de drenagem das águas pluviais nas frentes de lavra e nos pátios de estocagem, de forma a conduzi-las para tanques de decantação antes da liberação para o meio externo.
- Para o controle de poeira, instalação de barreira vegetal nos entornos da cava e do pátio de estocagem, e aspersão de água sobre os acessos não-pavimentados situados no interior e no acesso ao empreendimento.
Dependendo da situação topográfica, as medidas usuais de recuperação de cavas de argila envolvem:
- Preenchimento de cavas com materiais estéreis, e outros materiais disponíveis como resíduos de construção, terraplenagem para reafeiçoamento do relevo com a finalidade de atenuar o impacto visual, reduzir a possibilidade de erosões, permitindo a revegetação e, em certos casos, conversão das áreas para um novo uso.
- No caso de lagos remanescentes, estabilização de taludes marginais por meio de suavização dos cortes, seguido de revegetação.
Parcela importante das minerações ainda carece de práticas mais adequadas de controle e recuperação ambiental. Se as cavas individuais configuram degradações restritas, a aglomeração de empreendimentos em certas regiões tem provocado um impacto acumulativo considerável, sobressaindo, entre outros, processos de desmatamento, assoreamento de drenagem, formação de pequenos lagos, pilhas abandonadas de argila e de material estéril, e taludes expostos sujeitos à erosão. Em alguns núcleos oleiros, a precariedade técnica e a ilegalidade das operações de lavra colocam em permanente risco a sustentabilidade da atividade mínero-cerâmica. Uma solução estruturante possível, e que, como visto, já está sendo colocada em prática em alguns APLs, é a implantação de uma mineradora comum. Essa forma de condução empresarial da atividade mineral permite a concentração da produção de argila em poucas áreas e contribui para uma produção otimizada (ganho de escala), propiciando o controle e a recuperação das áreas mineradas e facilitando o processo de legalização das minas.
Agradecimentos
Os autores expressam seus agradecimentos ao Instituto de Pesquisas Tecnológicas do Estado de São Paulo e a Subsecretaria de Mineração da Secretaria de Energia e Mineração - SEM do Estado de São Paulo pelo suporte e financiamento do projeto “Estudo estratégico da cadeia produtiva da indústria cerâmica no Estado de São Paulo – Fase 1”, que gerou os resultados apresentados neste artigo.
Referências
ABC – ASSOCIAÇÃO BRASILEIRA DE CERÂMICA – Informações gerais na homepage. Disponível em: <http://www.abceram.org.br>. Acesso em: 05 de abr. 2018.
ANICER – ASSOCIAÇÃO NACIONAL DE CERÂMICA VERMELHA. Informações gerais na homepage. Disponível em: <http://www.anicer.com.br>. Acesso em: 08 de abr. 2018.
CABRAL JUNIOR, M.; SERRA, N. (Coord.) Bases para implantação de um Polo Mínero-Cerâmico no Estado da Bahia. Salvador: CBPM, 2006. 132 p.
CABRAL JUNIOR, M.; MOTTA, J. F. M.; ALMEIDA, A. S.; TANNO, L. C. RMIs: Argila para Cerâmica Vermelha. In: LUZ, A. B. da; LINS, F. A. F. (Org.). Rochas & Minerais Industriais: usos e aplicações. 2ed. Rio de Janeiro: CETEM/ MCT, 2009, p. 747-770.
CABRAL JUNIOR, M.; SUSLICK, S.; SUZIGAN, W. Caracterização dos Arranjos Produtivos Locais de Base Mineral no Estado de São Paulo: Subsídio à Mineração Paulista. Geociências (São Paulo. Online), v. 29, p. 81-104, 2010.
CABRAL JUNIOR, M.; GAMBA, T. de C.; TANNO, L. C.; ALMEIDA, A. S. Proposta metodológica para identificação e caracterização de fontes de suprimento de matérias-primas minerais: aplicação na indústria de cerâmica vermelha do Médio Rio Tietê - SP. Geociências (São Paulo. Online), v. 31, p. 287-307, 2012.
DNPM – DEPARTAMENTO NACIONAL DA PRODUÇÃO MINERAL. Anuário Mineral Paulista. 2016. Disponível em: <http://www.dnpm.gov.br>. Acesso em: 07 de abr. 2018.
FACINCANI, E. Tecnologia ceramica – I laterizi. Itália: Gruppo Editoriale Faenza Editrice. Faenza. Seconda edizione. 267p. 1992.
IPT - INSTITUTO DE PESQUISAS TECNOLÓGICAS DO ESTADO DE SÃO PAULO. Desenvolvimento de processo de fabricação de telhas de cerâmica vermelha especiais em ciclos rápidos de queima – fase I. São Paulo: IPT, (Rel. n. 92 351-205).
IPT - INSTITUTO DE PESQUISAS TECNOLÓGICAS DO ESTADO DE SÃO PAULO. Estudo estratégico da cadeia produtiva da indústria cerâmica no Estado de São Paulo – Fase 1. São Paulo: IPT, 2018. (Rel. n. 153900-205).
MOTTA, J.F.M.; ZANARDO, A.; CABRAL JUNIOR, M.; TANNO, L. C. e CUCHIERATO, G. As matérias-primas plásticas para a cerâmica tradicional: argilas e caulins. Cerâmica Industrial, vol.9, n.2, p.33-46, 2004.
MTE – MINISTÉRIO DO TRABALHO E EMPREGO. Base RAIS/TEM ano base 2016. Brasília: MTE, 2018.
SILVA, M.S. Da importância da cerâmica vermelha ou estrutural. Cerâmica, São Paulo, v. 28, n. 147, p. 21-25, 1982.
Deixe um comentário